NewPaakkola’s new conveyor system proceeds to 3D modeling
NewPaakkola has developed a conveyor system utilizing innovative technology for the dry stacking of tailings. This new technology enables significant progress in the green transition while offering substantial cost savings for customers. The system was launched in November at the Finnmateria 2024 trade fair in Jyväskylä. The product development process has now advanced to the 3D modeling phase, which serves as the foundation for design.
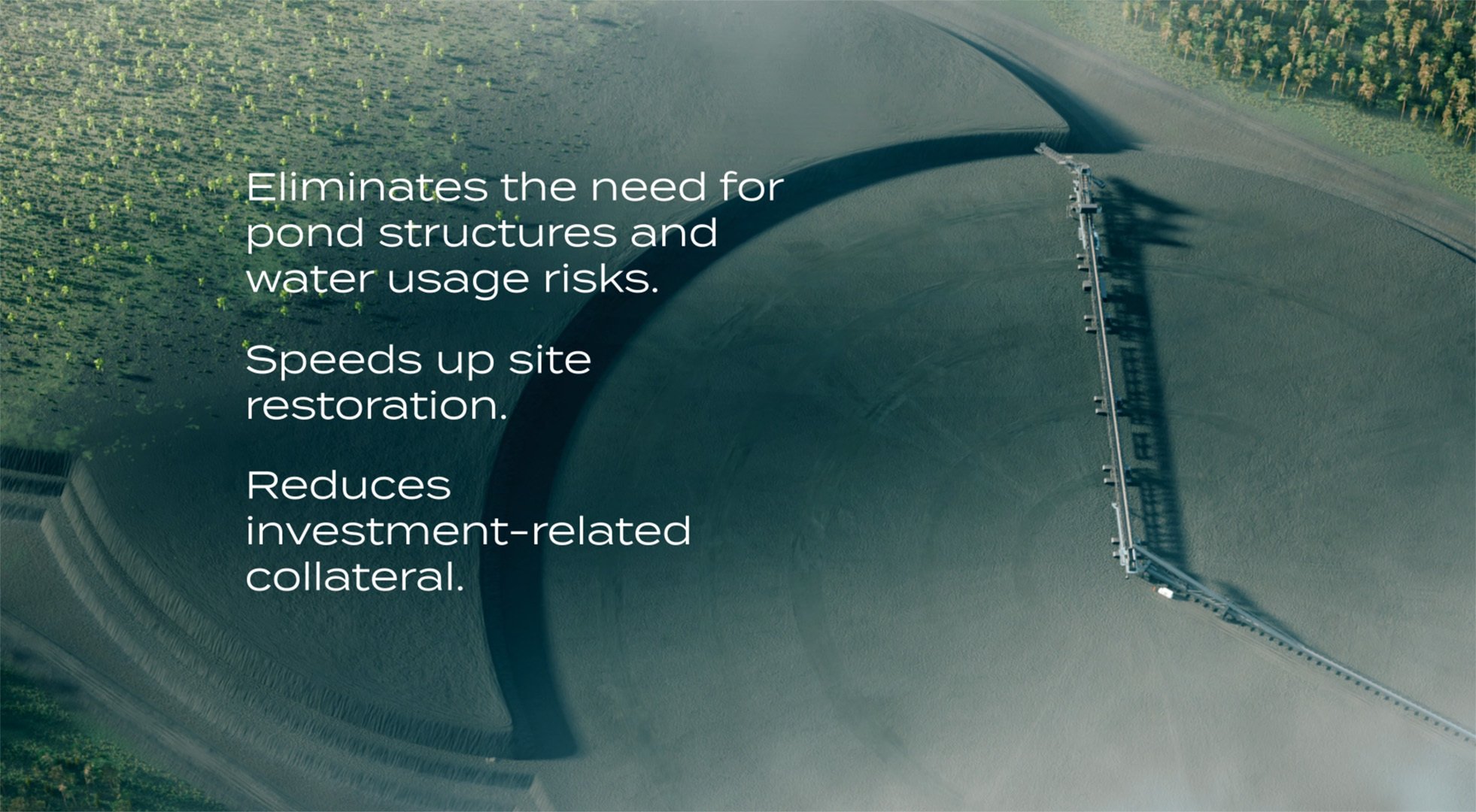
“At the beginning of the project, we define the capacity, speed, and load requirements, as well as select materials such as the belt, frame, motors, and rollers. The second phase involves conceptual design, where we create an initial draft or diagram of the conveyor structure, determine the belt’s length, width, and inclination, and select the power transmission system, including motor power and gearbox,” explains Product Manager Juha Teikari.
The 3D modeling process starts with the basic components (frame, belt, rollers), from which an initial frame model is created using CAD software (e.g., SolidWorks). Basic dimensions are set, and components are positioned. After this, detailed elements such as bearings, tensioners, supports, and protective elements are added. The motor and power transmission system are modeled, and attachment points and connections are verified.
“The next phase is mechanical analysis and testing, where structural strength analysis (FEA) is conducted to ensure durability, the belt’s movement and load distribution are simulated, and any potential weak points or design flaws are identified,” says Teikari.
Finally, the model is refined, and if necessary, exploded views of the components are created. Technical drawings for manufacturing are prepared, a bill of materials is compiled, and assembly, installation, and maintenance instructions are provided. If required, a 3D-printed or scaled-down prototype is built for testing. The prototype is tested under real-world conditions, and necessary improvements are made.
“After the 3D modeling phase, the conveyor system proceeds to production, where the manufacturing process is monitored. The system is installed, tested in its operating environment, and its performance is evaluated with adjustments made if necessary. This process ensures that the conveyor functions efficiently, safely, and meets the required standards,” concludes Juha Teikari.
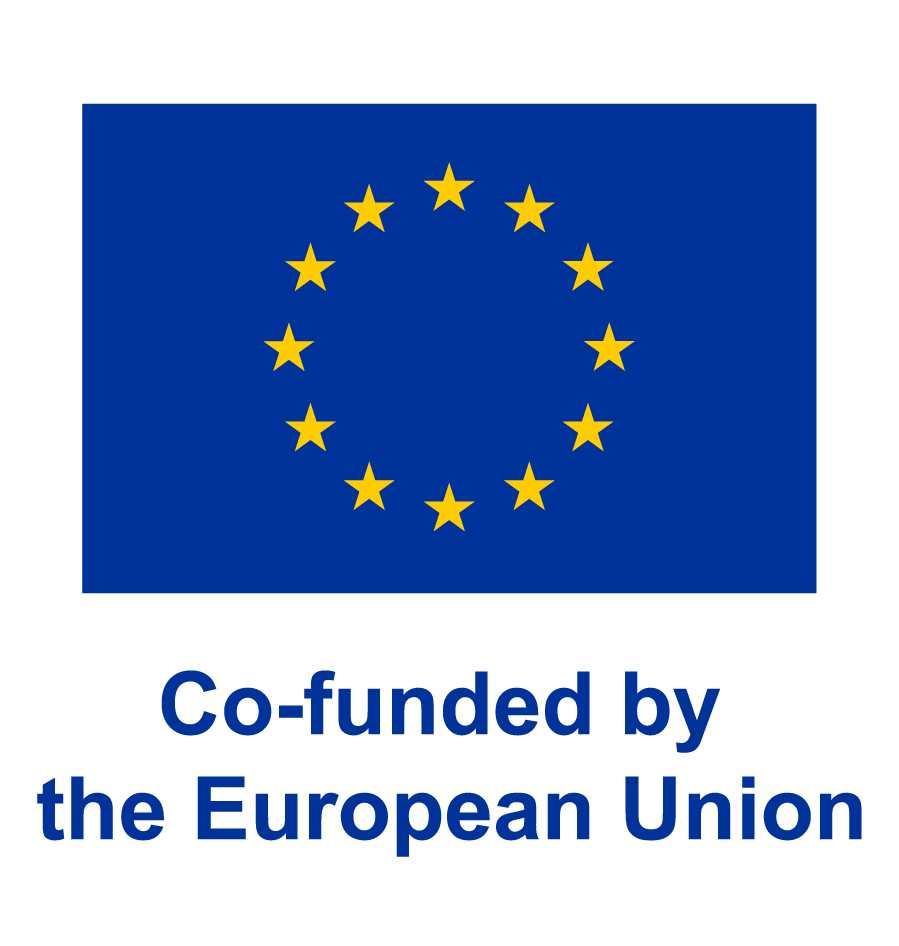
The development project aimed at international markets has been co-funded by the European Union, with funding granted by the North Ostrobothnia Centre for Economic Development, Transport and the Environment.